
光造形における各造形向きのメリットとデメリット(DF2/ideaMaker編)
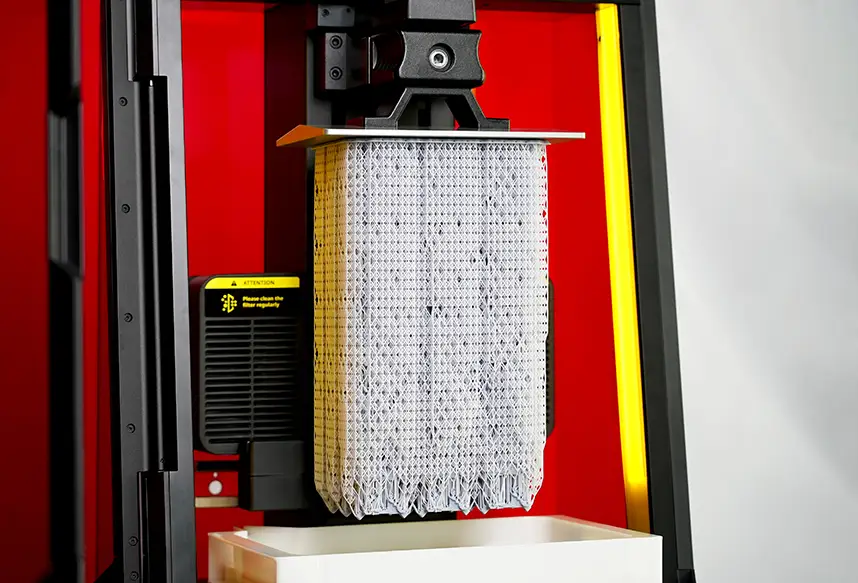
DLP方式やSLA方式などのレジンを使用した光造形方式の3Dプリンターはフィラメントを使用するFFF方式の3Dプリンターに比べ、3次元的なモデルの向きとなるパターンが多いのと同時に造形方式の関係でサポートの生成がほぼ必須になります。
その為、ユーザーはモデルの形状から造形安定性や意匠面の仕上がり、サポートによる後処理の手間などを考慮して配置するスキルが求められます。
今回はモデルの配置方向に関するメリットおよびデメリットについて紹介していきます。
本記事はメーカー純正の標準的なレジン(Raise3D Standard white)を使用した際の造形方向を参考としています。レジンの種類・材質によって得意とする造形方向は変化しますので予めご了承ください。
モデルをプリントベッドに対して垂直に配置
メリット
- サポートの設置個所が少ないことから後処理がしやすく、全体的な造形物の仕上がりが損なわれにくい。
- 1個当たりの造形面積が減る為、1度に複数個並べての造形が可能。
- サポートの出力量が比較的少ない為、造形コストが抑えられる。
デメリット
- レイヤー数が多くなり造形時間が増える
- サポートの接地箇所が少なくなり形状により脱落の懸念がある。
- サポートが少なく二次硬化でモデルの変形が起きる懸念がある。
- 造形箇所が一点に集中する為、レジンタンクのフィルムが局所的に劣化しやすい。
得意なモデル
- 筒や柱形状などの一方向に長いモデル
苦手なモデル
- ブロックなど断面積の広い大型のモデル
※造形担当者からのコメント
日本3Dプリンターではある程度の厚みがある板状のモデルや円筒形のモデルにこの配置をよく選択しています。
サポートが底面側にしか殆ど設置されない為、サポート除去や研磨などの後処理の手間が少なくサンプルの量産に適しています。
大型の物モデルは脱落の懸念があり非推奨ですが、モデルの中身を中空にするなどして断面積を減らすことで造形可能な場合があります。
モデルを斜めor 3次元的な角度に配置
メリット
- 造形安定性が高まり造形中、脱落などの失敗が少ない。
- サポートがモデルの広範囲に設置される為、二次硬化での変形が起きにくい。
- モデル表面に付着した未硬化のレジンが流れ出やすく洗浄効率が向上する。
- 垂直に配置した時よりもレイヤー数が減る為、造形時間が短縮できる。
デメリット
- モデルの多方面にサポートが付くため、後処理の手間が多い。
- ビルドエリアに対してモデルの配置がXY方向に広がる為、エリアに収まりきらない場合がある。
- サポート使用量が増える為、造形コストが掛かる。
得意なモデル
- ほぼ全てのモデル
苦手なモデル
- 意匠面が多方にあるモデル
※造形担当者からのコメント
ideaMakerの設定にある「方向の自動調整」機能では3次元的なこのパターンで配置されることが多く、DF2に限らず光造形ではポピュラーな造形配置です。
日本3Dプリンターでは主に大型のモデルや全体的に複雑な形状など剥離による失敗のリスクが高いモデルでこの方向を選択します。
前述の通りサポート除去と後処理の手間が多くなる為、自動サポート設定後に手動サポート設定で造形できそうな個所を1つ1つ削除しています。
モデルをプリントベッドに対して平行に配置
メリット
- 総レイヤー数が減り、短時間で造形が出来る。
- 穴形状などXY方向の寸法精度が安定する。
デメリット
- 断面積が広くなるため剥離抵抗の増加による失敗のリスクが高くなる。
- モデルの片側一面に多くのサポートが付くため、後処理の手間が多い。
- サポート面に未硬化のレジンが残留しやすく、また洗浄液が十分に行き渡りにくくなることから洗浄の手間が多くなる。
得意なモデル
- コネクタなど小型のモデル
苦手なモデル
- 断面積の広い大型のモデル。
※造形担当者からのコメント
日本3Dプリンターではこの配置は主に寸法精度を重視したモデルを造形する際に選択します。しかし、モデルのサイズが大きくなるとサポート面側に未硬化のレジンが残留します。残留した未硬化レジンが多いと通常の洗浄工程でも十分に落とせないことが多く、手間が掛かってしまいます。
以上のことから各造形方向にもメリット・デメリットがあり、造形安定性と仕上がりの向上と後処理による手間の削減を両立させるにはユーザーの経験値に大きく依存します。
最後に
自分の作りたいモデルの最適なモデル配置がまだ定まっていない場合は、無理に調整せず方向の自動調整機能に従ってスライスを行いましょう。
ideaMaker ver5.1.0から造形方向の自動調整機能が拡張され、様々な条件に応じた造形向きに自動で調整が可能となっています。
詳しくは弊社HPリリースノートを参照してください。