
巨大なサンゴを3Dプリントする試み
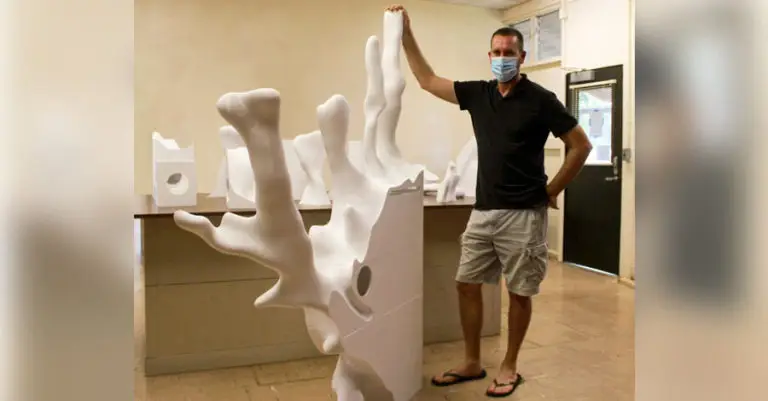
Raise3Dを使ってユニークな取り組みを行っているジョン・ゲーベル氏のケースを紹介します。
サンゴ礁をデジタル技術でアーカイブする
ハワイ大学教授のジョン・ゲーベル氏は、同大学の海洋チームと協力し、サンゴの生態を人々に理解しやすいように視覚化するプロジェクトを開始しました。このプロジェクトは、サンゴが海に与える影響、サンゴの種類や大きさの違いについて、議論を深めることを目的としたものです。
まず、海洋チームのジョン・バーンズ氏が、シュノーケリングの名所であるハワイ州プナのカポホで撮影したサンゴの画像をフォトグラメタリー技術で3D化します。カポホのサンゴといえば、30cm四方ほどの大きさの、カリフラワーサンゴの一種であるe.Mandrinusです。貴重なサンゴですが、2018年にキラウエア火山による溶岩流に見舞われ、e.Mandrinusが自生していたカポホの潮だまりは、現在完全に埋まってしまっているそうです。
このプロジェクトは火山噴火より前に始まりました。そのため、幸いにもチームは埋まってしまった地域に自生していたサンゴのサンプルを保存していました。
バーンズ氏はフォトグラメタリーで得たデータにVR技術を組み合わせて、噴火前にそこにあったはずのサンゴが、当時どんな風景だったかをVR空間で見られるようにしました。
ゲーベル氏の3Dプリンティング・プロジェクト
バーンズ氏のVRプロジェクトからインスピレーションを受けたゲーベル氏は、e.Mandrinusサンゴを実物よりも大きなサイズ(原寸の800倍)で3Dプリントするプロジェクトを開始しました。
彼の目標は、人々が両手を広げて触れるような大きなサンゴの模型を3Dプリントし、あたかも自分が魚になったようなスケールでサンゴを体感してもらうことです。彼は、3Dプリントされた実物よりも大きなサンゴが、サンゴ一般に対する人々の見方を変え、生態系で果たす役割について好奇心と議論のきっかけとなることを望んでいます。
このモデルをプロトタイプとして、将来的にはより大きなバージョンを作るために、現在6,000時間まで印刷を続けています。このプロジェクトをより大きなスケールで実現するために、彼は公共の場に常設し、子供たちがその上に登って体験できるようにすることを計画しています。
3Dプリントプロジェクトにe.Mandrinusサンゴが選ばれた理由
ゲーベル氏はこのサンゴを初めて見たときに「最もクールなサンゴの1つ」という印象を持ったといいます。さらに、このサンゴは視覚的に最も面白い特徴を持っていると説明しました。例えば、枝の数が最も多く、間隔が広く、葉が波打っているのが魅力的でした。視覚的な魅力に加え、全体的な構造から、拡大したときにインタラクティブになる可能性が最も高く、彼の将来の計画には最適な選択肢となりました。
制作プロセスと、ぶつかった壁を乗り越えるまで
ゲーベル氏は当初、バーンズ氏がフォトグラメタリーで作成したモデルをスライスして、そのまま3Dプリントしました。しかし、このプロセスでモデルを800倍に拡大すると、サイズに比してポリゴンの密度が低く、カクカクして見えてしまうことに気づきました。
ゲーベル氏は、3Dプリントの結果を改善するために、造形するパーツのサイズを変えてみることにしました。Burns氏のフォトグラメタリーモデルに戻り、それを4分の1にカットし、まずそれぞれのサイズを800倍にします。
次に、ゲーベルは、拡大した四分の一を100〜200個に切り分け、表面を再調整しました。その作業は、表面がなめらかになるよう再メッシュ・スムーシングし、位置合わせを行い、そしてまたスムーシング、というプロセスで行われました。
ゲーベル氏はこの作業を10回ほど繰り返して、ポリゴン数を50万ポリゴンまで上げ、きれいで滑らかなモデルを完成させました。そして、この滑らかなモデルをMeshmixerで組み立て直し、モデル全体を作り上げました。
より効率的な設計への変更
3Dプリントされたサンゴのパーツは、それぞれ約22.6kgと重いため、磁石で固定することはできません。そこでゲーベル氏は、パーツに穴を開け、手を伸ばして3Dプリントしたパーツを固定するための金具を追加することにしたのです。
このアクセスホールを作るために、ゲーベルはMeshmixerを使ってモデルをくり抜きました。彼は、くぼみのインフィルがどうあるべきかを学んで、適切な厚みがあり、かつ強度と軽さを兼ね備えたパーツを作りました。
3Dプリンターは、サポートを使用せずにアクセスホールのあるパーツを問題なく造形できました。ゲーベル氏は、垂直方向に造形すれば、サポートがなくともこれらの形状を造形できることを発見しました。これは非常に実用的なソリューションであったため、ゲーベル氏のプロジェクトではほとんどサポートを使用していません。
アクセスホールによって、ゲーベルはより少ないフィラメントで必要なパーツを作ることができるようになりました。以前は2つの大きな部品の造形で1巻のフィラメントを使いきっていましたが、今では1巻で4、5個の部品を造形できるようになりました。
サスティナブルなPLAフィラメント
ゲーベル氏がPLAを選んだ重要な理由のひとつは、PLAがバイオプラスチックであり、持続可能な資源であることです。彼のプロジェクトは、サンゴの生態系や海洋生物に対する人々の認識を変えることを目的としていたため、環境に優しい3Dプリント素材であることは重要でした。
また、PLAは、一般的に使用され、印刷しやすく、価格も手頃な3Dプリント材料です。このため、Goebelは、最初の印刷中にコスト効率の高い方法で構造設計を微調整する柔軟性を得ました。
「Raise3D Pro2 Plus」を選んだ理由
ゲーベル氏のプロジェクトの全過程は、前述の通り、実物よりも大きなサンゴを造形することでした。彼が3Dプリントして組み立てたサンゴのパーツは、彼の身長を超えます。そのため、彼が必要とするサイズのパーツを効率的に生産できる3Dプリンターが必要でした。
Pro2 Plus(※販売終了。現在は後継となるRaise3D Pro3 Plusをご案内しています。)は、ゲーベル氏が必要とする寸法の高品質造形を確実に作成できる大型プリンターです。価格も手頃で、様々な製品との比較と予算の検討した上で、ゲーベル氏はPro2 Plusを導入することに決めました。
Raise3D Pro2 Plusは、最大0.01mmの積層ピッチが実現可能で、サンゴモデルの造形精度を十分に満たします。また、305×305×605 mmの大型造形サイズが造形できるため、サンゴのような大きいパーツの分割造形回数を有効に減らし、組み立ての作業も大幅に節約できます。
Pro2 Plusの後継機となるRaise3D Pro3 Plus
Proシリーズの最高峰となる最新機種
最高の完成を迎えるために
「72個出来ていて、あと125個から200個くらいかな。まだまだこれからです。」とゲーベルは語ります。最終的な組み立て工程は、現在行っているのと同じように、モデルをスライスし、1/4インチのボルトで結合します。設計変更の甲斐あって、すべてのアクセスホールを使って、内部まで手を伸ばしてボルトを締め付けることができます。
しかし、3Dプリントしたサンゴをさらによいものにするために、現在のモデルをもとに、組み立てる前に一つひとつ塗装し、完全に組み上げた後に手直しをすることを想定しているそうです。また、自然界にはカラフルで美しいサンゴが生息しているので、健康なサンゴのように見えるように、テクスチャを追加することも考えています。
ゲーベル氏に、完成したサンゴを最終的にどのような場所に設置したいかを尋ねると、「図書館です」と力強く答えました。図書館では、3Dプリンターで造られたモデルに触れ、その姿をよく見ることができます。
「図書館には膨大な図書のほか展示物もありますし、多くの人が訪れます」
ゲーベル氏は、図書館に設置することで、自分のプロジェクトをより多くの人の見てもらえることにワクワクしています。
ご購入、企業に関するお問い合わせ はこちら
03-3520-8928 【受付時間】09:00〜18:00(土日祝除く)